The Impact of Prototype Mold Manufacturers on Modern Business
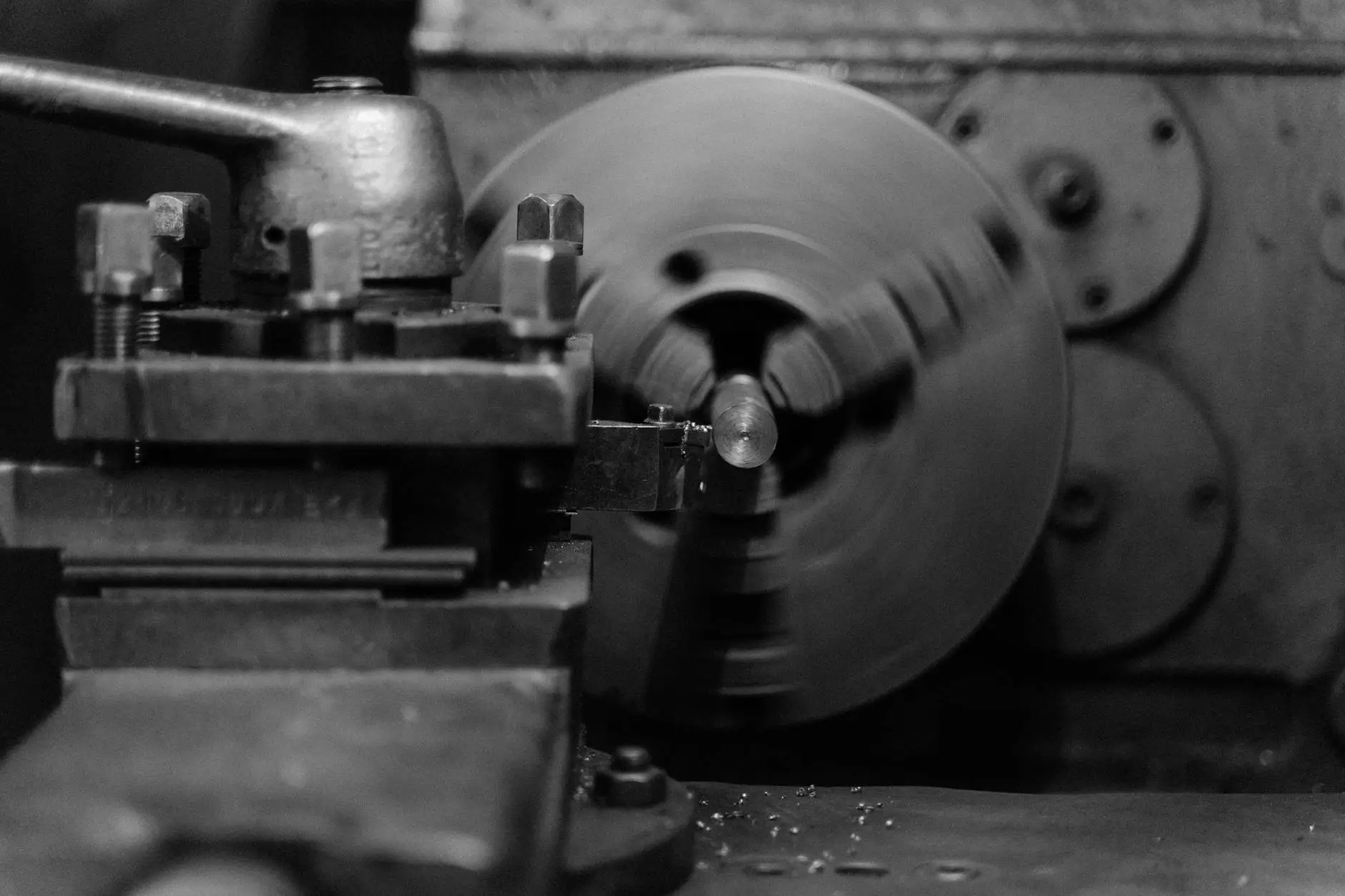
In the rapidly evolving landscape of manufacturing, prototype mold manufacturers play a crucial role in driving innovation and efficiency. These specialized companies are essential for businesses that rely on custom parts, prototypes, and tooling solutions. This article explores the dynamics of prototype mold manufacturing, its significance in various industries, and how companies like Deep Mould are shaping the future of product development.
Understanding Prototype Mold Manufacturing
At its core, prototype mold manufacturing involves creating molds that are used to produce parts or products in their initial stages. This process is vital for any business that wants to ensure quality and performance before moving into full-scale production. The benefits of using prototype molds include:
- Cost Efficiency: Creating a prototype allows for testing and adjustments without the financial burden of full production.
- Time Savings: Quick turnaround on prototypes helps businesses bring products to market faster.
- Enhanced Design Accuracy: Prototypes allow for real-world testing and modifications, ensuring that the final product meets specifications.
The Role of Metal Fabricators in Prototype Mold Production
Metal fabricators are integral to the process of creating high-quality prototype molds. These professionals utilize a range of techniques to turn raw materials into finished molds that can withstand the demands of production. Key processes include:
1. CNC Machining
Computer Numerical Control (CNC) machining involves the use of computer-controlled machines to create precise molds from metals. This technology allows for intricate designs and consistent quality across multiple copies. With the expertise of metal fabricators, prototype mold manufacturers can deliver unparalleled accuracy.
2. Welding and Assembly
Welding techniques are often necessary to assemble various components of a mold. Skilled metal fabricators can ensure that all pieces fit together seamlessly and maintain structural integrity during production runs.
3. Surface Finishing
The finishing of molds is crucial for producing high-quality parts. Techniques such as polishing, anodizing, and coating enhance the durability and performance of the molds created. This is where prototype mold manufacturers excel, as they offer both functional and aesthetic enhancements to their products.
Innovative Techniques in Prototype Mold Manufacturing
As technology advances, so too does the methodology surrounding prototype molds. Here are a few cutting-edge techniques that modern prototype mold manufacturers employ:
1. 3D Printing
3D printing has revolutionized the way prototype molds are designed and produced. It allows for rapid prototyping, reducing lead times significantly. Manufacturers can quickly iterate on designs, leading to faster production cycles and the ability to adapt to client feedback swiftly.
2. Injection Molding for Prototypes
Injection molding is not solely reserved for mass production. Many prototype mold manufacturers utilize this technique to create initial prototypes efficiently. This allows companies to test materials and designs under real-world conditions, dramatically reducing the risk of production issues in later stages.
3. Advanced Simulation Software
Simulation software plays a pivotal role in mold design and testing. By creating virtual models, manufacturers can analyze the behavior of a mold under various conditions, leading to better designs and less material wastage.
Choosing the Right Prototype Mold Manufacturer
Selecting a prototype mold manufacturer is a critical decision that can influence the success of your project. Here are some factors to consider when selecting the right partner:
- Experience: Look for manufacturers with a proven track record in your industry. Their experience ensures they understand the specific challenges and requirements you may face.
- Technology and Equipment: Ensure the manufacturer utilizes modern technology and equipment that can meet your project's needs.
- Quality Assurance: Evaluate their quality control processes to ensure that the molds produced meet both your specifications and industry standards.
- Customer Support: A manufacturer that provides excellent customer support will ease communication and help address any issues that may arise.
The Future of Prototype Mold Manufacturing
The future of prototype mold manufacturers is bright, with continuous advancements in technology reshaping the industry. Here’s what we can expect:
1. Integration of AI and Machine Learning
Artificial Intelligence (AI) and machine learning will streamline processes, enhancing predictive analysis for mold performance and adjusting designs based on simulation outcomes. This integration will greatly accelerate production timelines and improve overall efficiency.
2. Sustainable Manufacturing Practices
With an increasing focus on sustainability, prototype mold manufacturers will adopt practices that reduce waste and energy consumption. Processes such as recycling scrap materials and using eco-friendly substances in production are expected to become more prevalent.
3. On-Demand Manufacturing
The shift towards on-demand manufacturing models will allow businesses to produce only what they need, minimizing excess inventory. This trend aligns well with modern business practices that emphasize lean operations.
Case Study: Deep Mould
As an exemplary player in the field, Deep Mould has harnessed modern technologies and methodologies to emerge as a leader among prototype mold manufacturers. Their commitment to quality, innovation, and customer satisfaction sets them apart in a competitive landscape.
Innovative Solutions
Deep Mould offers a diverse array of solutions tailored to meet specific client needs. From rapid prototyping to full-scale production, they leverage advanced technologies to ensure the highest standards of excellence.
Customer-Centric Approach
Understanding that each client has unique requirements, Deep Mould prioritizes a customer-centric approach. They work closely with clients through every stage of the development process, ensuring transparent communication and satisfactory outcomes.
Industry Leadership
With years of experience, Deep Mould has built strong relationships across a variety of industries, including automotive, aerospace, and consumer goods. Their expertise not only accelerates product development but also drives innovation across sectors.
Conclusion
In conclusion, prototype mold manufacturers like Deep Mould are essential contributors to the advancement of manufacturing processes. By providing crucial services in the product development cycle, they allow companies to innovate, respond to market demands, and enhance operational efficiency. As the industry continues to evolve, embracing new technologies and practices will empower businesses to thrive in a competitive marketplace.
As you consider the possibilities for your next project, remember the pivotal role that selecting the right prototype mold manufacturer can play. A partnership with a reputable manufacturer can be the difference between a mediocre product and one that stands out in the market.