Understanding LEV Inspection in South Wales
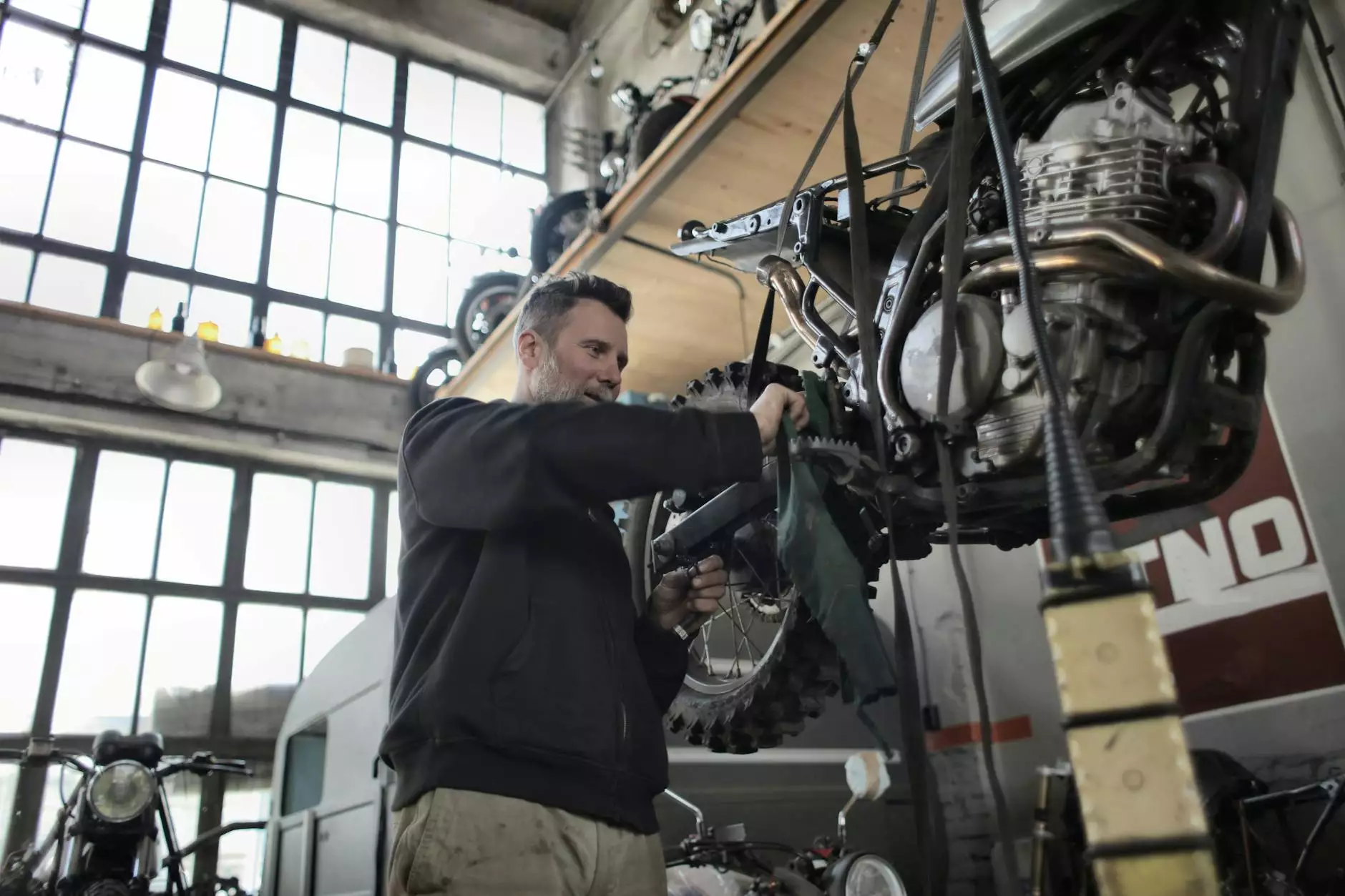
Local Exhaust Ventilation (LEV) inspections play a crucial role in ensuring safety and compliance within various industries. In South Wales, businesses are increasingly prioritizing the health and safety of their employees, particularly in environments where hazardous substances are used or generated. This article provides an in-depth look at the importance of LEV inspections, the regulations governing them, and the benefits companies can gain from regular inspections.
What is LEV?
Local Exhaust Ventilation (LEV) systems are designed to capture and remove airborne contaminants from the workplace. These systems are essential in industries such as manufacturing, woodworking, and metalworking, where dust, fumes, and other harmful substances can lead to serious health problems. The primary purpose of LEV is to maintain air quality and protect employees' health by reducing their exposure to hazardous substances.
Why Are LEV Inspections Important?
Regular LEV inspections are vital not only for compliance with health and safety regulations but also for promoting a culture of safety within the workplace. Here are some of the key reasons why these inspections are essential:
- Health Protection: Minimizing exposure to harmful substances helps reduce the risk of respiratory issues and other long-term health effects.
- Regulatory Compliance: South Wales businesses are required to comply with specific health and safety regulations, including those set forth by the Health and Safety Executive (HSE).
- Equipment Efficiency: Regular inspections can identify issues with the LEV system, ensuring it operates efficiently and effectively.
- Cost Savings: By addressing potential issues proactively, businesses can avoid costly downtime and repairs.
- Employee Morale: A safe working environment fosters a positive workplace culture and boosts employee morale.
LEV Regulations in South Wales
In South Wales, LEV inspections are governed by several key regulations, including:
- The Health and Safety at Work Act 1974: This act places a duty on employers to ensure the health, safety, and welfare of their employees.
- The Control of Substances Hazardous to Health (COSHH) Regulations 2002: COSHH requires employers to assess risks from hazardous substances and implement control measures, including appropriate LEV systems.
- The Provision and Use of Work Equipment Regulations (PUWER) 1998: These regulations require that equipment used at work, including LEV systems, is safe and properly maintained.
The LEV Inspection Process
Understanding the LEV inspection process is crucial for businesses in South Wales. Here’s how it typically unfolds:
1. Pre-Inspection Preparation
Before the inspection, it’s essential to gather relevant documentation, including: - Previous inspection reports - Maintenance records - System design specifications
2. Visual Inspection
A qualified inspector will conduct a thorough visual examination of the LEV system. This includes:
- Checking the condition of ductwork and hoods
- Assessing the integrity of the fans and motors
- Inspecting filters and ensuring they are clean and functional
- Evaluating air flow and capture efficiency
3. Performance Testing
After the visual inspection, performance testing is conducted. This may involve:
- Measuring air flow rates
- Testing for adequate extraction velocities
- Confirming that the LEV system meets the required standards for air quality
4. Reporting and Recommendations
Once the inspection and testing are complete, a detailed report is compiled. This report typically includes:
- Findings from the inspection
- Performance data
- Recommendations for any maintenance or upgrades needed
Benefits of Choosing Safe Plant UK for LEV Inspections
When it comes to LEV inspections in South Wales, partnering with an experienced company like Safe Plant UK provides numerous benefits:
1. Expert Knowledge and Experience
Safe Plant UK employs qualified professionals with extensive knowledge of LEV systems and regulatory requirements. Their expertise ensures that inspections are conducted accurately and in compliance with all relevant regulations.
2. Tailored Solutions
Every business has unique needs. Safe Plant UK offers customized solutions tailored to your specific operational environment and requirements, ensuring optimal performance of your LEV system.
3. Comprehensive Services
From installation and maintenance to regular inspections, Safe Plant UK provides a full range of services that cover all aspects of LEV management. This holistic approach simplifies compliance and ensures your systems remain effective over time.
4. Commitment to Health and Safety
A partnership with Safe Plant UK demonstrates your commitment to maintaining a safe working environment for your employees. This commitment not only meets regulatory requirements but also enhances your company's reputation within the industry.
How Often Should LEV Inspections Be Conducted?
The frequency of LEV inspections depends on several factors, including:
- The nature of the substances being handled
- The level of risk associated with those substances
- The operational environment and usage patterns
As a general guideline, it is recommended to have a full LEV inspection at least once every 14 months. However, businesses should evaluate their specific circumstances and, if necessary, conduct inspections more frequently.
Common Issues Found During LEV Inspections
During inspections, several common issues may be identified, including:
- Duct blockage due to dust accumulation
- Inadequate air flow rates
- Faulty fans or motors
- Worn-out filters
- Improper system design or installation
Identifying and addressing these issues promptly is essential for maintaining system efficiency and ensuring workplace safety.
LEV Inspection Case Studies in South Wales
To illustrate the significance of LEV inspections, here are a couple of case studies reflecting the experiences of businesses in South Wales:
Case Study 1: A Local Woodworking Shop
A woodworking shop in South Wales faced concerns about air quality due to excessive wood dust. After conducting a comprehensive LEV inspection, Safe Plant UK discovered significant blockages in the ducting system. Following their recommendations, the shop implemented a regular cleaning schedule and upgraded their LEV system. Post-implementation, air quality tests showed a remarkable improvement, leading to a safer working environment and improved employee satisfaction.
Case Study 2: A Metal Fabrication Company
A metal fabrication company was struggling with compliance issues related to fume extraction. Safe Plant UK carried out an in-depth inspection and identified insufficient extraction rates in certain areas. They provided targeted recommendations, including the installation of additional hoods and fans. The company acted promptly, resulting in enhanced air quality and full compliance with health regulations.
Final Thoughts on LEV Inspections in South Wales
In summary, LEV inspection in South Wales is not just a regulatory requirement; it is a critical component of creating a safe and productive work environment. Businesses must prioritize regular inspections, ensure compliance with the relevant regulations, and partner with reputable service providers like Safe Plant UK. By doing so, they can protect the health of their employees, enhance their operational efficiency, and solidify their commitment to workplace safety.
For more information or to schedule an LEV inspection, visit safeplantuk.co.uk today!
lev inspection south wales