Mastering the Art of Injection Molding Shops: Your Gateway to Quality Plastic Parts
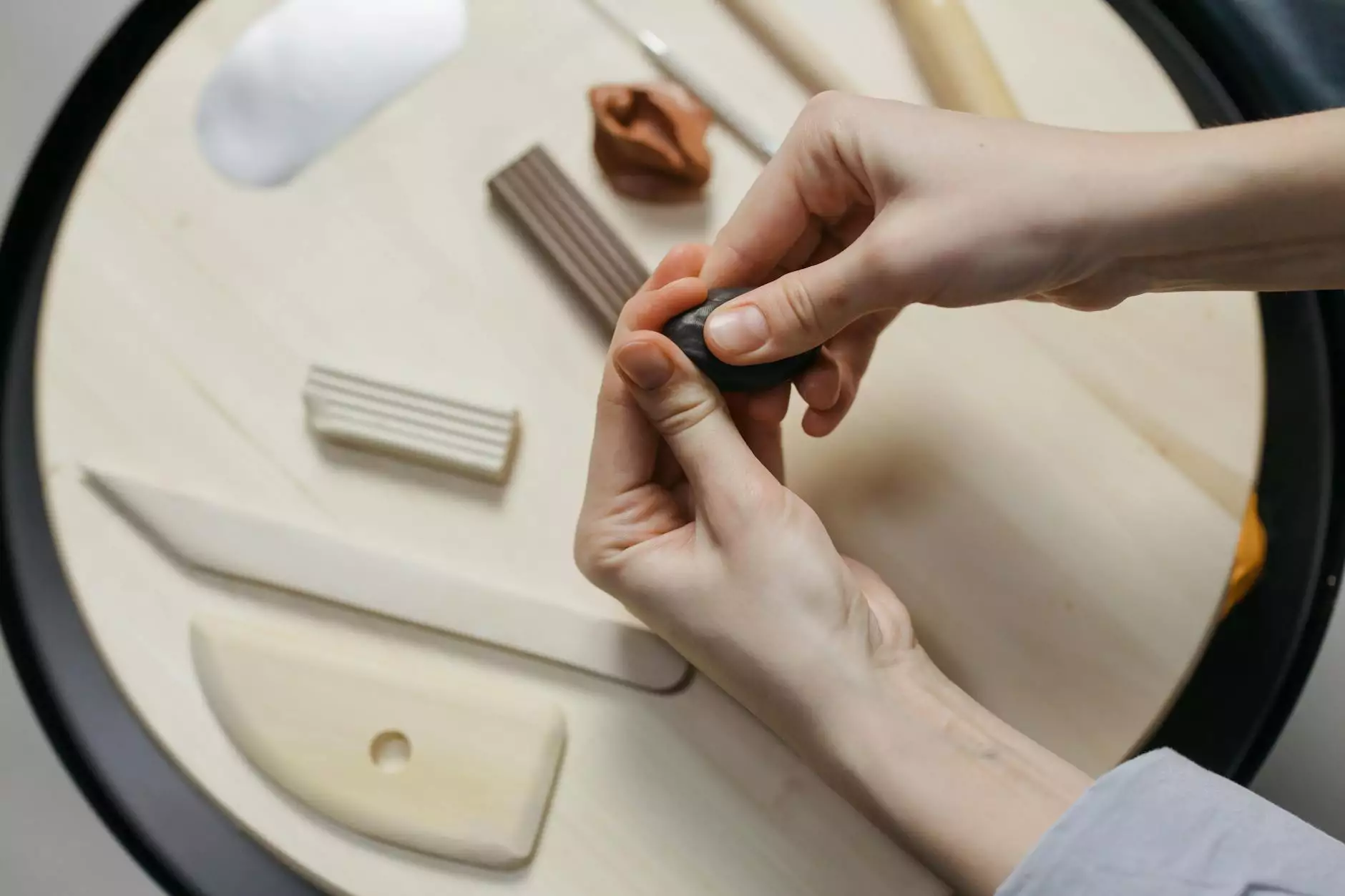
In today's manufacturing landscape, businesses are increasingly turning to injection molding shops as a means to streamline production processes and ensure high-quality output. Injection molding is a versatile and efficient method that allows manufacturers to produce intricate parts with precision, speed, and consistency. This article dives deep into the workings of injection molding, the pivotal role of plastic mold makers, and how to select the right injection molding manufacturer for your business needs.
Understanding Injection Molding
Injection molding is a process where melted plastic is injected into a mold, allowing it to cool and solidify into the desired shape. This technique is widely used in various industries, including automotive, consumer goods, electronics, and healthcare, due to its capability to produce large volumes of parts with minimal waste.
The Benefits of Injection Molding
- Efficiency: Injection molding shops can produce thousands of identical parts simultaneously, making it ideal for large-scale production.
- Cost-Effectiveness: While the initial investment for molds may be high, the per-part cost decreases significantly as production scales up.
- Precision: Advanced molding techniques allow for tight tolerances and complex geometries, leading to high-quality finished products.
- Versatility: A wide range of materials can be used, including various plastics and composites, catering to diverse industry needs.
Plastic Mold Makers: The Backbone of Injection Molding
Plastic mold makers play a crucial role in the overall success of injection molding shops. They are responsible for designing and manufacturing the molds that shape the final products. Their expertise directly influences the quality and efficiency of the production process.
What to Look for in a Plastic Mold Maker
Choosing the right plastic mold maker is essential for ensuring the success of your injection molding projects. Here are some key factors to consider:
- Experience: Select a mold maker with a proven track record in the industry. Experience often translates to better quality and faster turnaround times.
- Technical Expertise: The ability to work with advanced materials and technologies is vital. Ensure the mold maker is well-versed in the latest methods and trends.
- Customization Capability: Your projects may have unique requirements. A good mold maker should be able to customize molds according to your specifications.
- Quality Assurance: Look for a mold maker that implements rigorous quality control measures at every stage of production.
Injection Molding Shops: Services Offered
Injection molding shops provide a spectrum of services that extend beyond mere molding. Here are some common offerings:
1. Mold Design and Prototyping
Using CAD software, injection molding shops can design and prototype molds, allowing for adjustments before manufacturing. This step is crucial for identifying potential issues early in the process.
2. Injection Molding Processing
This involves the actual injection of plastic into the molds. Skilled operators ensure optimal temperatures and pressures are maintained for the best results.
3. Secondary Operations
To achieve a final product, many parts require secondary operations such as trimming, painting, or assembling. Quality injection molding shops provide these services in-house to streamline processes.
4. Quality Control and Testing
Ensuring that every part meets the required specifications is essential. Reputable injection molding shops conduct thorough inspections and testing to maintain high standards.
How to Choose the Right Injection Molding Shop
With numerous injection molding shops available, selecting the right partner for your business can be daunting. Here are some strategies to help you make an informed choice:
1. Assess Their Portfolio
Review the past projects of the injection molding shop. This can give you insights into their capabilities and specialties, helping you determine if they can meet your unique requirements.
2. Read Customer Reviews
Feedback from previous clients is invaluable. Look for testimonials that highlight the shop's reliability, communication, and overall quality of service.
3. Consider Location and Lead Times
Proximity can reduce shipping costs and lead times. Evaluate potential partners based on their geographical location and their ability to meet your delivery requirements.
4. Evaluate Communication
Clear communication is key to a successful partnership. Ensure that the injection molding shop you choose is responsive and willing to engage in collaborative discussions.
The Future of Injection Molding
The future of injection molding is set to be driven by technological advancements and innovations. Here are a few trends shaping the industry:
1. Automation and Robotics
The integration of robotics and automation within injection molding shops is revolutionizing the manufacturing process, enhancing efficiency and reducing labor costs.
2. Sustainable Practices
As environmental concerns grow, more injection molding shops are adopting sustainable practices. This includes using recyclable materials and minimizing waste during production.
3. Enhanced Material Applications
Advancements in material science are leading to the development of smarter, more durable plastics that can withstand higher temperatures and pressures.
4. Digital Manufacturing
The rise of digital technologies like 3D printing, combined with traditional injection molding, is creating opportunities for more flexible production methods.
Conclusion: Harnessing the Power of Injection Molding Shops
In summary, the world of injection molding shops offers incredible potential for businesses looking to optimize their production capabilities. By understanding the intricacies of plastic mold making and injection molding processes, you can make informed decisions that lead to superior product outcomes. Whether you are a startup or an established company, investing in the right injection molding partner is crucial for achieving your manufacturing goals.
With the right strategy and a commitment to quality, your business can leverage the advantages of injection molding to stay competitive and innovative in a rapidly evolving market.